企业的竞争力来自于产品的高质量和低成本,而 汽车车身的质量和成本在很大程度上是在模具开发阶 段就基本确定了,因为在此阶段的产品方案、工艺方 案、模具准备方案等决定了模具成本、冲压件材料利 用率、生产效率、冲压件质量等。所以,在车身冲压 件模具开发阶段进行有效的成本控制和质量管理是非 常重要的。
1 模具开发阶段的成本控制和质量管 理的内容
1.1 成本控制 在不需要进行设备投资的情况下,模具开发阶 段的成本控制内容不仅包括模具、检具等工装的一次 性投资费用的控制,更包括了产品投产后的运行成本 即可变成本指标的控制,如冲压件材料消耗、生产效 率、废品率等指标。因为通常情况下,这部分成本占 产品成本60%以上。此阶段对成本的影响因素主要有 以下几方面。 (1)产品结构 不同的产品结构方案其成本差别是非常大的,在 满足功能的前提下,要尽量采用简单结构。 (2)工艺方案 不同的冲压成形方法(如是否采用落料、是否成 双生产、采用拉延成形还是压弯成形等)对成本的影 响都很大,而不同的工序数、检测方法等则直接影响 了工装的投入。
1.2 质量管理 模具开发阶段的质量管理包括模具质量管理和冲 压件产品质量管理。此阶段对质量的影响因素不仅包 括产品结构方案、工艺方案和模具结构,还包括对各 阶段的质量目标和过程的管理、控制情况。
2 模具开发阶段的成本管理和控制 模具开发阶段一般都是通过项目管理的形式来进 行成本管理和控制的。在保证满足质量、周期等要求 的前提下,对项目实施过程中所发生的费用,通过计 划、组织、控制和协调等活动实现预定的成本目标, 并尽可能地降低成本费用。主要通过技术(如产品与 工艺方案制定时的比较和选择)、经济(如核算)和 管理(如过程组织管理、各项规章制度等)活动达到 预定成本目标。项目的成本管理应贯穿于整个项目的 过程,其内容一般包括成本预测、成本控制、成本核 算、成本分析等。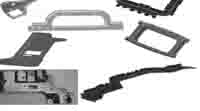
2.1 确定成本控制目标 首先要进行成本预测,这是成本计划的基础,为 编制科学、合理的成本控制目标提供依据。 (1)掌握产品的质量特性,以及所要达到的质 量目标和产量目标。这个基本前提掌握后,通过与国 内外模具厂家技术交流、让对方提供工艺方案和报 价,对各家方案进行对比分析,结合以往项目的经验并充分考虑质量和经济性的关系等,综合分析确定模 具费用控制目标。 (2)运行成本控制,此时要考虑到生产时成本 目标的控制。冲压件的材料利用率是生产运行成本的 重要指标,而产品结构形状和工艺方案决定了材料的 利用情况,应综合考虑产品特点和以往车型经验给出 经济合理的材料利用率目标,将该目标值作为技术要 求参数提供给模具制造单位,并在后期的具体工艺和 模具方案中按此目标进行管理和控制。
2.2 分析预测成本控制的风险 项目成本目标的风险分析,就是对在项目实施过 程中可能影响成本目标实现的因素进行事前分析,并 采取措施进行防范。模具项目中成本增加 的最大风险来自于产品的变更。根据以往 的经验,在模具设计制造过程中,产品的 变更是避免不了的。特别是在一个全新的 车型准备时更是如此。为避免由于产品变 更带来的成本失控或产生主机厂甲乙双方 的矛盾纠纷,影响项目的正常进行,在签 订合同和技术协议时要对产品更改的处理 进行特殊的说明。一般情况,合同价格中 都应包含一定的产品更改费用,在合同中 应明确规定合同价格中所包含的产品更改 范围。这样既能控制成本,又能保证一般产品和工艺 更改的顺利实现。同时,应对模具准备过程中的重大 产品更改进行严格控制,凡是对费用有较大影响的更 改应经过主机厂主管部门的审核。
2.3 控制生产运行成本 项目的成本控制,不仅要考虑一次性的模具投 资,更要考虑今后生产时的运行成本,因为冲压件的 模具成本仅仅是其中一部分,冲压件材料成本是主要 部分,同时还要考虑模具的维修、设备利用率等。在 工艺方案设计和模具结构设计中决定了这些方面的以 后成本,所以在项目的实施过程中要在保证质量的前 提下,时刻注意这些影响成本的因素,尽量达到降低 成本的目的。 在产品结构和工艺方案中要充分考虑材料利用率 问题。产品结构和工艺方案决定了材料利用率,要想 提高材料利用率,降低材料消耗,必须在这两方面下 功夫。 (1)设计产品结构时要尽量避免废料太多的形 状,这类零件的材料利用率很低,如图1。产品设计 人员往往只从功能上考虑,较少关心材料利用率问 题,这时工艺人员要及时将主机厂要求反馈给设计 者。对这类零件的解决方案:可以在设计上考虑将零 件分成几部分,然后将它们再焊接在一起;采用激光 拼焊板冲压零件;如果实在不可分,尽量考虑利用结 构废料。 (2)对一些功能要求简单的零件如加强板横梁 等,结构形状要尽量简单,这样可以用简单的压弯工 艺代替复杂的拉深成形工序,不仅可以节省模具投 资,还可以降低材料消耗,提高材料利用率。 (3)在满足产品功能要求的前提下,有些内部 件尽量用落料、压弯工序而不用成形工序,以降低材 料消耗,如图2。 (4)在工艺编排和模具设计时要考虑废料的回 收和利用。如某载货车后围窗口,按正常工艺生产, 其废料被切断后应从废料输送线自动排除,但考虑该 件废料利用价值很高,在模具设计时规定将该件的废 料不要切断并从设备的侧面滑出,使该件的废料得到 回收和利用,如图3。 图1 材料利用率低的零件 生产装备 2 0 1 0 年第3 期汽车工艺与材料 AT&M 39 P R O D U C T I O N E Q U I P M E N T (5)在编排工艺时需要综合考虑模具成本和 材料成本。如有的零件不用落料模也能生产出合格 件,这样可节省1套模具费用;但如果采用落料工序 可以节省材料的话,则需要进行综合计算。通常对 于大批量汽车生产来说,后期生产节省的材料费用 可能要远远高于模具成本,这时就应从长远考虑增 加落料模具。
|